Health & Safety - February 21, 2020
Good evening all.
I just want to thank Guy Suttonwood for all his efforts with the health and safety team and a very happy retirement
Over the last few months its been a very challenging time for the health and safety team and our executive members. I'd like to take this time to explain all the trouble we have encountered.
First off, I would like to start with our lead vacuuming in the oil temper. During our J.H.S.C meeting we were told that the lead vacuuming was going to be done during the showdown. At the beginning of December we were assured that it was scheduled and was still being done. We all came back from our Christmas break it wasnt done. After some investigation and being lied to that the company had cancelled, we found out that it wasn’t scheduled at all! On January 28th the lead vacuuming took place, although it wasn't finished the company has until Feb 28th to complete it. The company has started sending guys out for working at hight training so we can vacuum ourselves during shut downs.
Lead levels in the oil temper have been on the rise the past few years. Irene and I have been working on a lead program that will benefit our workers and make sure lead levels start to decline. Irene ordered new lockers for oil temp people to keep an extra pair of boots in the oil temper area for when they skim.
We started to organize and schedule all three lines skimmed and PM on the same day to limit the exposure rather than have the exposure in the mill every Tuesday. For some reason our general manager doesn't think health and safety matters regarding this situation and stopped the progress on this plan. Irene has also hired a cleaning company to clean up the oil temper lunchroom, there is a lot of oil and lead dust in the lunchroom that needs to be taken care of. Lastly, all oil temper personnel will now be given 10 pairs of coveralls due to the fact after a skim day we never have enough.
61,62,30 and 31 Frames was also vacuumed and 1.5 ton of soap was sucked up and disposed. My understanding of this whole situation is that they still have a bit of work to do but they have completed what the ministry order said and did the rails above these frames.
The glove issue came into light November 29th when all the wire drawing gloves were pulled from the vending machine. Our general manager had a cost cutting agenda and turned to health and safety to make some cuts. They went to a much cheaper glove, in which he didnt consult with the J.H.S.C and took it upon himself to bring in these new gloves. This situation has now been rectified and gloves now suitable for the tasks have been distributed. If you have any trouble with your gloves please feel free to bring forward any issues to either your health and safety team or any of your stewards.
Hoist Rails have been an issue since Maxime the head of health and safety for Arcelormittal shut them down on January 31st. Over the past 2 days we have held tool box meeting before every shift to shed some light on this frustrating situation. There was alot of rush, confusion, and poor communication on the companies part and hopefully moving forward we will have good communication and understanding of what is going to take place. In general, they have 1 month (March 13th) to repair the cracks, replace the rails completely or shut the machines down until one of the first 2 options have been completed. All the scheduled p.m days will be displayed on the boards up front.
Just something to keep in mind, it's your right to refuse unsafe work. Dont let your foreman try to convince you to something you feel unsafe.
Andrew Chetwynd
Local 5328
H/S Chairman
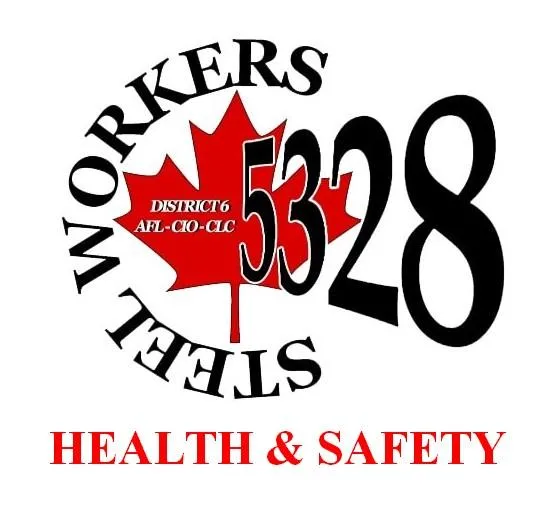